R&D Whitepaper: Oxygen Impurity Control for Reactive and Refractory Metal Alloys Produced on a Plasma Gas Atomizer
Oct 15,2024
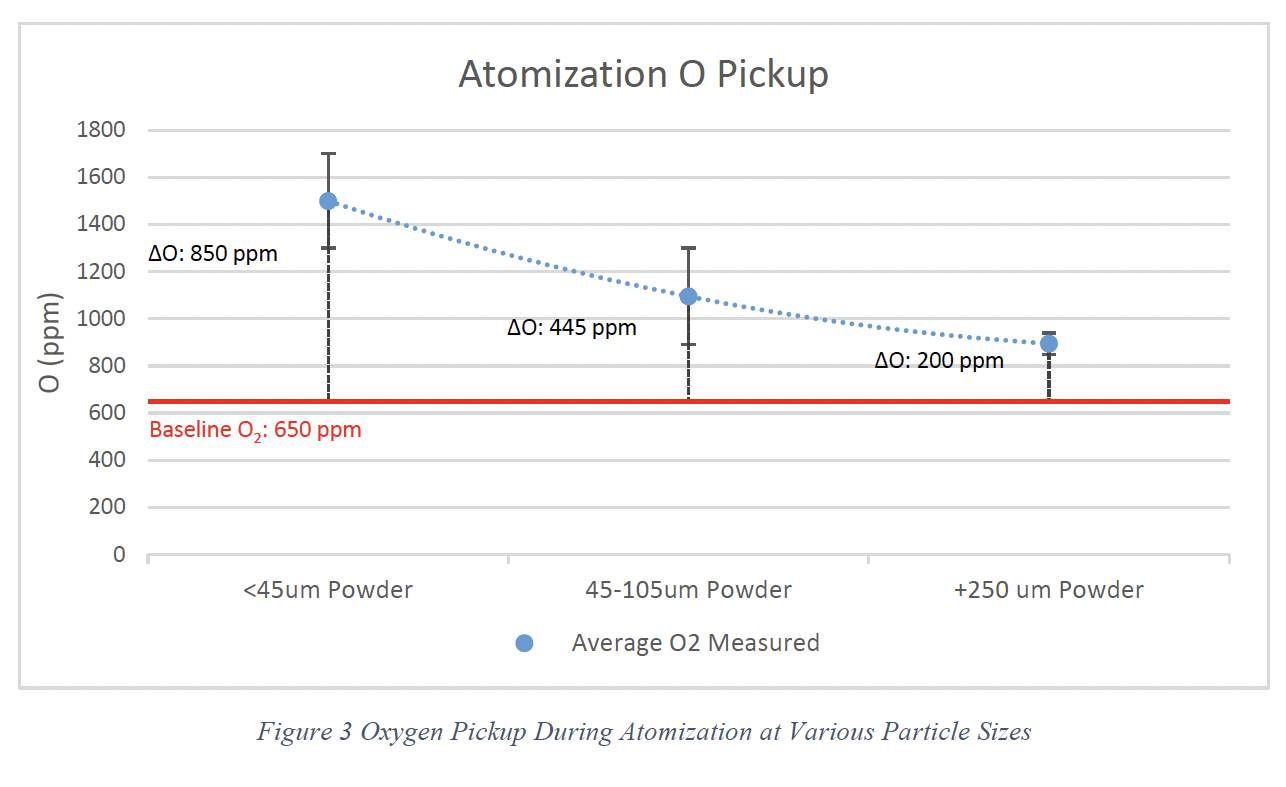
Authors: Aamir Abid, Matt Stone, Michael Jacques, Geof Dusky, Bryce D’Alba, Francis Butry and Michael Wojcik
Abstract: A barrier to the broader adoption of refractory and reactive metal powders (like titanium and its alloys) is the stringent control of the chemistry of AM-suitable powders. The addition of interstitial gases such as oxygen, nitrogen, carbon, and hydrogen can influence the processing of powder via AM and will significantly alter the mechanical properties of the printed part. Plasma Gas Atomization (PGA) is a proven technology to produce production-scale refractory and reactive metal powders. Plasma melting allows for the introduction of a broad range of feed materials including revert without incurring the additional cost of processing feed to wire or bar forms. In this study, we investigate the sources of oxygen pickup or reduction throughout the atomization process. The evolution of oxygen levels is measured, starting at the feedstock, following through the atomization process, and finally at the product packing stage. The sources of increase or reduction of oxygen are presented and discussed.
Click to read the R&D whitepaper
Talk To An Expert About Developing Your Powder Metal Production Process